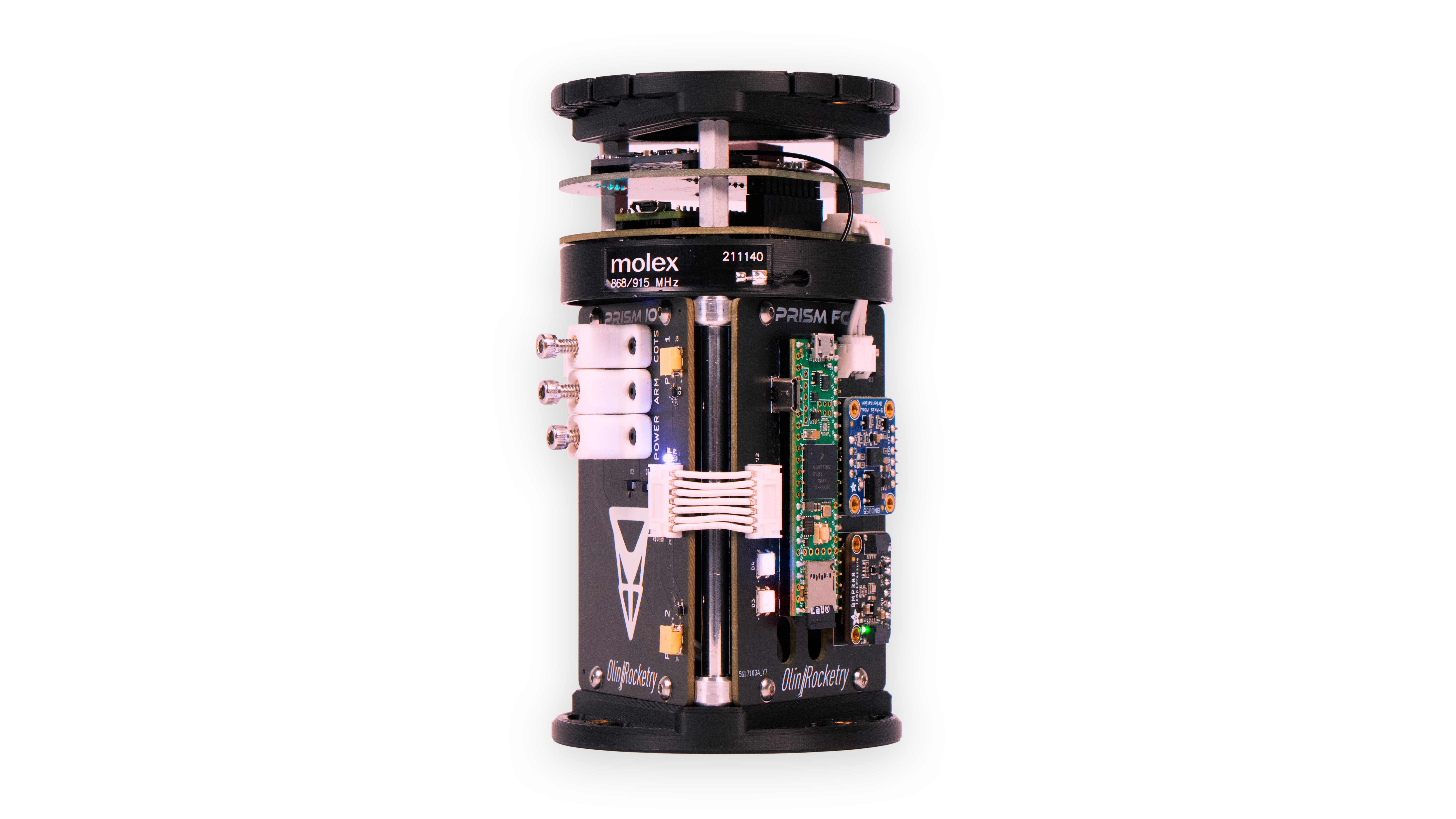
Model Rocket Avionics
A full-featured avionics suit developed for high-power model rockets
A playful spin on a clastic tool using principles from mass production.
There were four primary project goals:
The two halves of the injection-molded knife case are joined with press-fit bosses to facilitate toolless assembly and repair. I ran plastic flow simulations to predict weld lines, identify air traps, and refine part geometry and gate placement to improve moldability. I then used 3D CNC milling to machine the molds from aluminum blanks and made injections using a Morgan-Press G100-T. Despite some cosmetic sink marks, the parts met all functional requirements.
The aluminum grip clips over the plastic case and engages with the blade thumb stud.
A flexure built into the base of the grip provides resistance and a tactile snap when the blade locks.
The sheet metal blanks were bent with custom form tools and then powder coated.
Costing less than $4 per unit in materials and labor, the design met all of the project requirements and gave me an opportunity to apply DFM principles to an actual marketable product!
A full-featured avionics suit developed for high-power model rockets
A custom dimable LED desk light
Meet my fleet of self-built multirotors